认 证:工商信息已核实
访问量:2030276
耐驰(上海)机械仪器有限公司 2014-04-02 点击4982次
最新干法工艺-
突破了以往干法粉碎无法企及的细度极限!
过去,对于绝大多数干法研磨工艺,2微米是该类工艺的实际极限值。在最新的S-Jet®工艺中,流化床气流磨内使用过热蒸汽作为研磨气体。该种蒸汽气流磨可以生产d50在130纳米,并且最大粒径不超过400纳米的干粉,突破了以往干法粉碎无法企及的细度极限。
提升产品性能和开发新产品的动力长期存在,然而,往往因为很小的问题造成巨大的阻碍。寻求创新不断驱使着众多涂料、颜料及相关行业研发者关注细微颗粒(被研磨到1微米甚至更细的物料)以提升产品性能或开发新应用。
在多年前,微米颗粒的生产已成为现实,并带来众多益处。
介质研磨工艺,即使用研磨珠(介质)来将大颗粒磨细,目前在上述行业工艺内扮演着举足轻重的角色。这一工艺的典型过程是将物料分散在悬浮液中,使用带介质研磨设备去研磨或分散物料,最后再通过干燥以获取纳米颗粒。
以上每一过程都消耗能量并且会带来物料污染和设备的磨损。然而,由于在过去,干法工艺在生产纳米颗粒方面受限于产能,不得不通过湿法工艺来进行生产。这使得许多物料无法被大规模生产并限制了创新。
对于亚微米或纳米范畴内更精细的干粉产品的需求带来了对于全新研磨工艺的研发。通过干法来纳米化颗粒带来了节能以及经济性。不同于传统的气流磨,S-Jet®系统使用过热蒸汽作为研磨气体。使用蒸汽作为研磨气体在简单的不带有内置分级轮的螺旋式或环式气流磨内已被使用多年。 然而,在这一最新的系统内,内置了空气分级轮以精确控制颗粒粒径。这两个因素使得蒸汽流化床气流磨可被商业化。
例如,从下表两个例子中可以看到,在过去使用传统干法研磨加工d99小于2微米的氧化铁颜料是非常困难的,但是在最新的S-Jet®蒸汽系统内,其细度可达到d99小于1微米。
样品名称 | 细度 | |
d50 µm | d99 µm | |
氧化铁 | 0,13 | 0,37 |
陶瓷颜料 | 0,13 | 0,34 |
相较空气,蒸汽可以为气流磨提供更高压力。更高的研磨压力产生了更高的气流速度。在绝对压力40bar的状态下,气流速度约可达到1200米/秒(更高的压力仍具可能性,并将更有益)。与空气最高约600米/秒速度相比,喷嘴处的动能大约提高了4倍。研磨能量的增加使得在研磨过程中可产生更细的颗粒,并将颗粒输送到分级轮区域。
作为动态分级颗粒的一种介质,蒸汽可确保获得相较空气更细的切割点。蒸汽的特性,诸如相较空气更低的动态粘度和比重,以及更高的声速,使得在分级轮内可产生一个更高的流速。因此,作用于待分级物料的加速力更大,切割点更细。由于更高的气流能量,获取更细的颗粒本身已经可实现,以上的作用是通过干法工艺生产纳米颗粒的关键点。
S-Jet®这一最新技术开启了研发者和工程师对于新应用和材料的思考。新市场和机会也随着新材料出现。
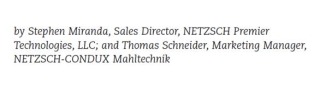
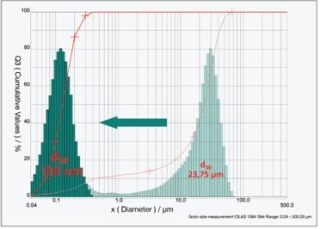
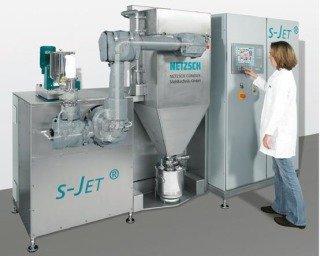